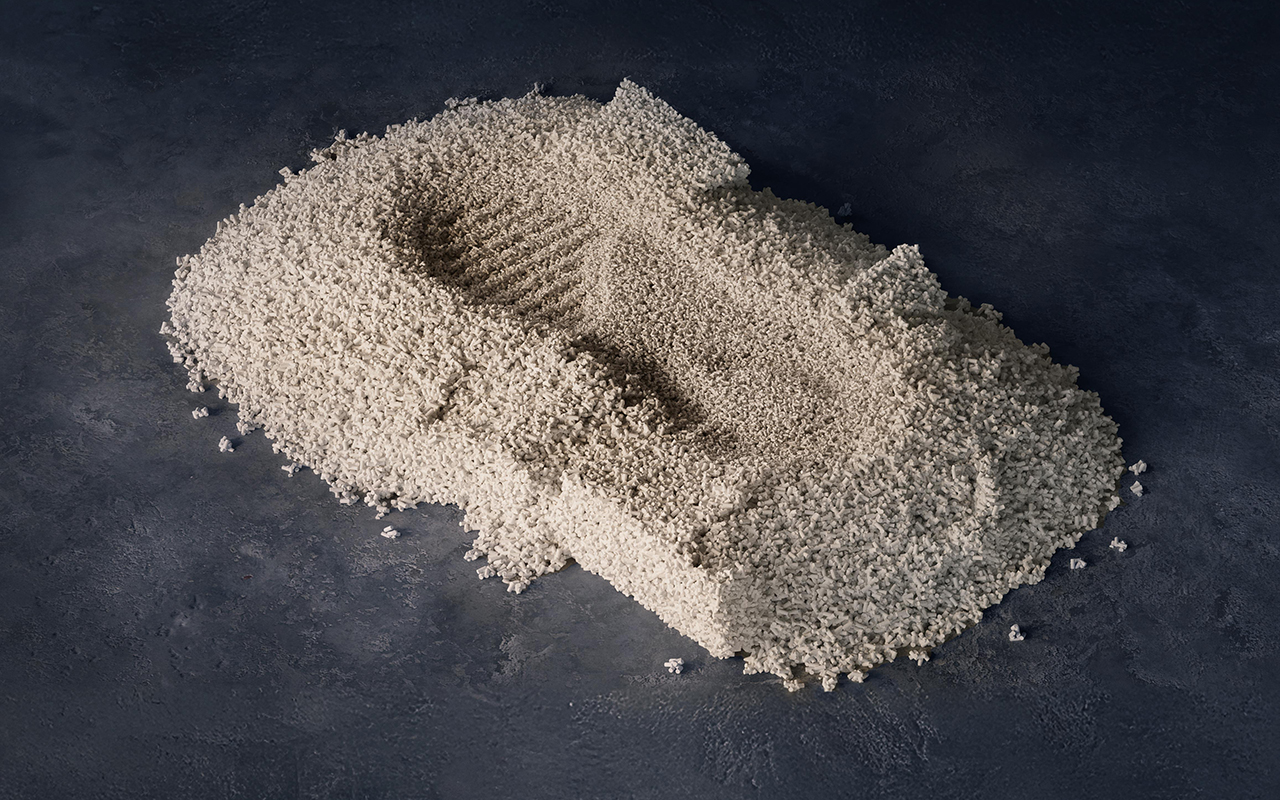
Circular economy company Syklo to commercialise state-of-the-art biocomposite internationally
Finnish Circular economy company Syklo has bought 100% of the share capital of biocomposite company Elastopoli. The acquisition reinforces Syklo’s investments in advancing the circular economy in line with its growth strategy. The company’s goal is to achieve an even higher degree of circular economy rate and to refine recycled materials into more valuable products.
Elastopoli is a pioneer in the production of pulp-based cellulose biocomposite and has patented its technology worldwide. The technology enables the production of high-quality biocomposites, which can be used to extensively replace technical plastics and glass fibre composites, among other things. Recycled cellulose pulp and plastic can be utilised as raw materials for biocomposites, significantly increasing the processing degree of recycled raw materials.
“Elastopoli is a great example of an amazing excellence there is operating in the field of circular economy. They have developed a unique, patented technology that genuinely solves the challenges faced by customers in the plastics industry. Their technology is internationally scalable and their biocomposite has the best technical properties on the market. The product can also be piloted and tailored to meet specific customer needs. Elastopoli is not merely a research and development company; they already serve large international clients who are eager to purchase more biocomposites than the pilot plant in Sastamala can currently produce,” says Teemu Koskela, managing director of Syklo Oy.
The patented technology has been tested and developed in Elastopoli’s pilot plant in Finland for several years. With the acquisition, Syklo has also made an investment decision to develop the pilot plant’s existing production line and increase its production capacity. The investment will triple the production capacity of the pilot line. After that Syklo plans to build a commercial-scale biocomposite plant in conjunction with Finland’s largest plastic recycling plant in Hyvinkää. The plastic recycling plant and the biocomposite plant have excellent synergy, as the recycled plastic feed for the biocomposite production line will be sourced from the plastic recycling plant. When completed in 2025, the biocomposite plant will produce 8,000 tonnes of biocomposites annually for the use of the plastic industry. After this, Syklo’s goal is to triple production by 2029 and expand to larger production units after that.
“We have a long history in biocomposite research and development. We have developed and patented a biocomposite production method that transforms recycled fibres into biocomposite with recycled plastic using a wet process, resulting in excellent technical properties for our customers’ biocomposite products. The process also enables the direct integration of recycled fibre waste into production, while recycling process water and process waste back into the system. Sidestream waste, such as plastic and metal, is then recovered as side stream products for further use” says Markku Nikkilä, managing director at Elastopoli Oy.
“Now is an excellent time to secure additional resources for our operations. Syklo’s strong commitment to advancing a genuine circular economy convinced us that they are who we want to start commercialising this technology with,” Nikkilä continues.
“As the new owner, we warmly welcome all of Elastopoli’s employees, current customers, and partners with great enthusiasm. In line with our growth strategy, we are committed to further developing and growing our operations,” states Koskela.
Elastopoli Oy will become Syklo Biocomposites Oy as of 1/1/2025.
Contact information
Teemu Koskela, Managing Director, Syklo Oy
teemu.koskela@syklo.fi
+358 (0)50 400 8721
Markku Nikkilä, Managing Director, Elastopoli Oy
markku.nikkila@syklo.fi
+358 (0)50 540 8922
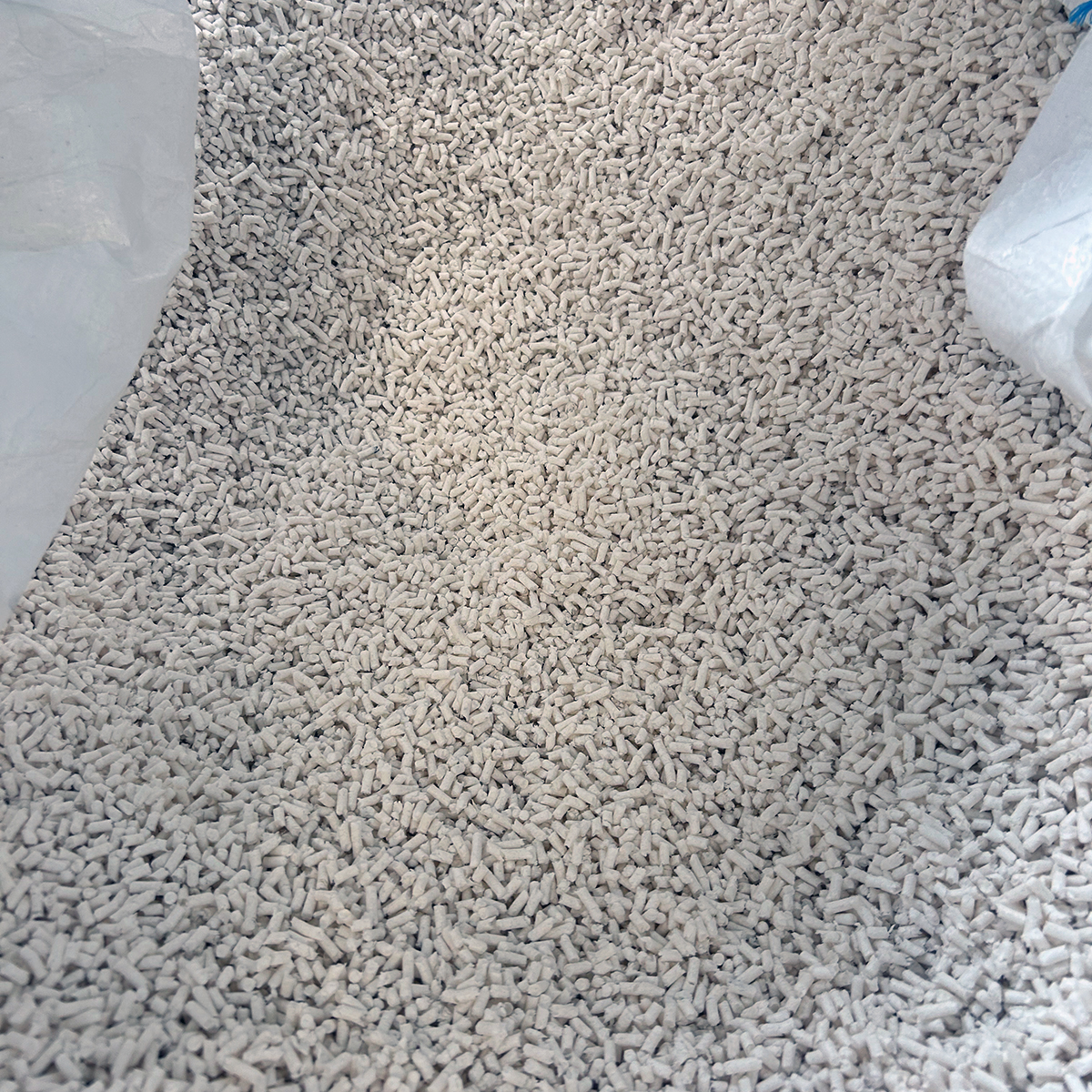
Syklo’s biocomposite – advanced technology for reinforced materials
Syklo’s biocomposite is used to reinforce technical plastics in applications demanding improved tensile and flexural strength, as well as impact resistance. Thanks to this material, traditional reinforcements such as talc or glass fibre can be replaced with more environmentally friendly alternatives.